Noark Electric Highlights Their Breaker Modification Center
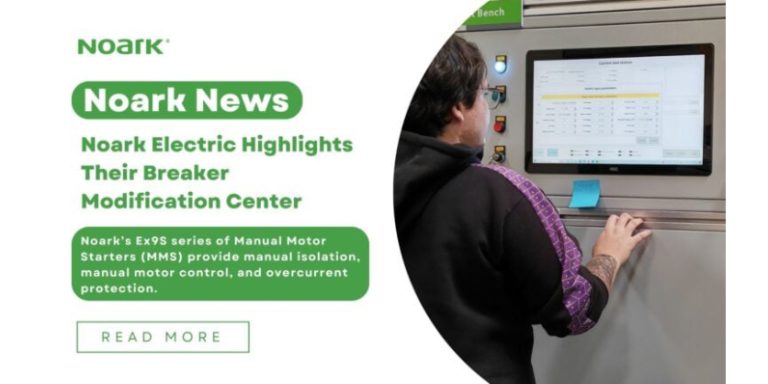
August 15, 2023
Mod Center is Expanding to Better-Serve Electrical OEMs Across North America
Noark Electric is a global manufacturer of low-voltage electrical components for industrial applications and their specialties involve motor control and circuit protection products for original equipment manufacturers (OEMs). Their entire portfolio of products is designed for ease of manufacturing and assembly.
Each component is developed in-house by their engineering team to meet the strictest standards and performance requirements and is covered by their exclusive five-year limited warranty.
Noark Electric is well-known for their world-class manufacturing and rigorous testing of their products that meet or exceed the highest performance standards in the industry. What should be better known is their ability to rapidly modify or produce products that satisfy their customers’ unique specifications. In this article, Rob Farrell, Marketing Director of Noark Electric, and Robert McKean, Assembly Technician at the Noark Power Breaker Modification Center discuss the Mod Center and how it is expanding to better serve electrical OEMs across North America.
What Does Noark Electric’s Modification Center Offer?
“We call it a ‘Modification Center,’ but really, what we are doing is building a new product through the Mod Center. We source a breaker from our parent factory that is configured up to a certain point, and then we add to it the things that make it unique to the customer specification. When we talk about modifications, really what we are talking about is the production of a new product,” explains Farrell.
Rob Farrell, Marketing Director of Noark Electric
These modifications are done out of Noark’s California-based warehouse location. As Noark’s primary distribution center, this location ensures prompt and reliable deliveries of their entire product range to customers all over North America. McKean runs the Breaker Modification Center and is responsible for everything from taking orders to building and shipping breakers. He explains how Noark can provide not just exceptional products for their customers, but also customized solutions.
“We will get requests from our distributors who have customers looking for a specific setup for an Air Circuit Breaker, or maybe smaller modifications on Molded Case Circuit Breakers as well. And, after talking about what their needs are, and seeing if we’re able to do that with what we have in inventory here, we make any adjustments that we need. We keep close contact with a lot of our customers.”
How Does Noark Ensure World-Class Quality?
Noark’s experts maintain a close relationship with their clients to ensure that they get the exact product they need. From the initial conversation about the order and the specific customizations, through to installation and troubleshooting once installed in the field, Noark has services in place to provide their customers with the highest quality products, backed with world-class service and support.
Starting with a quality product minimizes future troubleshooting when modifications are done. Noark’s products are safe and reliable from the start; their production plants are certified according to ISO standards to satisfy the highest demands in terms of quality assurance and production quality. Additionally, Noark also meets the stricter CIG 203 certification. When McKean receives a Molded Case Circuit Breakers (MCCB) or Air Circuit Breaker (ACB), for example, he already knows he is starting with a quality item that meets or exceeds certification standards.
And once it is modified to meet unique customer specifications, it is rigorously tested again to ensure it is safe and reliable. Using Noark’s A32 Power Circuit Breaker as an example, McKean explains the strict testing that each modified product is put through.
“For the A32s, once they are built, they are put into an automated test cell that tests just about every component that we put into it. For example, with the motor operators, it’ll test them at different levels of their control voltage down from 70%, 90%, and then 110% of its rated control voltage. It’ll do the same test with the trips that may be in it, our shunt trip, closing trip, under voltage trip. Then it’ll test the Trip Unit that’s attached to it. It’ll do a long, short, instantaneous, and ground fault test on them.”
Robert McKean, Assembly Technician at the Noark Power Breaker Modification Center
McKean adds, “If any errors come up during that test, that’s when I work to troubleshoot these issues and figure out whether it’s the component, or an issue with the ratings that were entered for the test. Breakers don’t leave the mod center until they’re able to pass the test completely.”
What Does the Modification Center Mean for Noark’s Future?
The Breaker Modification Center is expected to expand to support electrical OEMs with more products. One area of growth that Farrell is noticing is in the energy industry. He sees growth in applications that involve energy storage and transmission. He says, “For end applications like energy storage and solar and wind projects, primarily the former two, the trend in the industry is to push the voltage levels up for Molded Case and Power breakers. We are now introducing a new series of 800 Volt AC breakers, and we have plans to bring some of our existing products up to that level. Ultimately, we would like to get to 1000 Volts, and I think we are headed that way.”
Right now, the product range for the breakers modified and tested at the Center is typically under 800 Volts; however, upgrades have been underway to prepare the test center for new products that will be rated for higher voltages.
“Right now, the product range is from 800 to 4000 Amps. Most of the products are 600 Volt rated. The new products will be rated up to 800 Volts AC as they come out,” explains Farrell. To prepare the Breaker Modification Center for this upgrade, their team of engineers was able to work remotely on the test machines to update some of the programming and parameters. He adds, “It is a fully automated test cell that was built by the product engineers that designed the product.”
Rob Farrell, Marketing Director of Noark Electric
Typically, Noark aims for one-to-four weeks for an order of up to five breakers. Orders larger than that would be pushed to their main factory and planned with more lead time due to the size and complexity of larger projects. Maintaining these lead times, Noark’s Breaker Modification Center serves all of Canda and the US, with occasional customers in Mexico.
Their expansion of the Mod Center positions Noark with a unique advantage in the market. With only a small handful of other manufacturers providing 880 Volt to 1000 Volt products, Noark maintains a competitive edge. Farrell says, “Not enough people know that we have the capability to produce a breaker in a week if need be. That is unique in North America right now. Most manufacturers are in that six-to-eight-week timeframe to produce a breaker like the one that we are doing.”
He adds, “We started with the A32 power breakers, but we are also adding a new line of Enclosed Molded Case Breakers within the next month or so, and then we are going to expand that to be more generic modifications and adding accessories to our products.”