Vineland’s Omar Abdelzaher Discusses His Career and System Integration in the Horticulture Industry
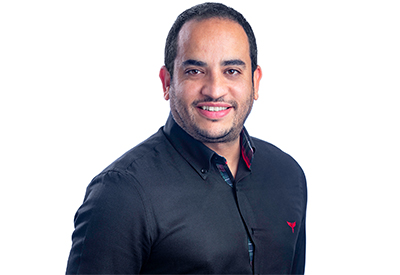
Sept 11, 2019
By Blake Marchand
Omar Abdelzaher is a Systems Integration Project Manager with an impressive resume thus far in the industry. Currently, he leads the Robotics & Automation – Systems Integration team, a new venture for Vineland Research and Innovation Centre (Vineland). His experience working in various sectors, including a pedigree of innovation in those positions as well as his experience in a research capacity with Texas A&M University, made his position at Vineland a perfect fit for both parties.
Omar studied Mechanical Engineering in Egypt where he earned his B.Sc. in 2003. Before taking his current position, Abdelzaher held positions with some high-profile organizations, in addition to developing several patented technologies.
“After graduation, I obtained a professional certification in Applied Mechatronics from one of the top technological institutes in Egypt, affiliated with the government,” he told Panel Builder & Systems Integrator.
In 2005, he earned his master’s degree in Applied Mechatronics, studying in Germany.
“During my master’s thesis, I worked at a garage door opener manufacturer as a Mechanical Development Engineer, where I had the opportunity to develop two novel conceptional designs and publish two patents from the concepts I developed. They have been commercialized through a big partnership agreement with a leading European manufacturer of these types of operators.”
Early on his career, Abdelzaher established a high pedigree for his potential. Which he would continue after accepting a position with Siemens AG in Frankfurt as a Mechanical Development Engineer. With Siemens he designed and developed medium voltage switch-gear assemblies. It was valuable experience, he said, “which gave me my first industrial high-tech manufacturing experience as well as a good exposure to LEAN manufacturing and Six Sigma procedures.”
His experience with LEAN manufacturing would become an asset in his work in the horticulture/agriculture industry, which he would aid in optimizing production facilities and minimizing waste to help maximize profit margins and revenue.
Abdelzaher would move on to work with Texas A&M University as a Research Assistant on a three-year research project, “developing a downhole logging access tool for a top oil and gas company in the Gulf area,” he said, “which ended up generating a couple of international patents, a number of publications and a commercialized downhole tool.”
Following that successful stint, he was granted a three-year graduate research assistantship, again with Texas A&M, working on various projects related to downhole mechatronics and drill strings vibration dynamics. As a result, he earned his second master’s degree, this time from Texas A&M in Mechanical Engineering.
“I then joined Halliburton, as a Technical Professional Engineer at their main Technology Center in Houston, continuing on the same track in developing subassemblies of various downhole LWD tools, gaining industrial experience in designing and developing downhole high-pressure/high-temperature mechatronics systems throughout their different product life cycle,” Abdelzaher told PB&SI.
Omar gained some valuable management experience working with an engineering services and consultancy firm based in the U.S. and Egypt as a Mechanical Engineering Manager. In that role he gained further experience working in automation and productions process optimization, material handling systems, project management, and LEAN manufacturing.
Working and studying in Egypt, Germany, Texas, and now working in Canada for Vineland, Abdelzaher has accumulated a wide range of experiences across different markets and cultures. That diverse range of perspectives and experience base is a crucial aspect to innovation. Which undoubtedly has contributed to his success with Vineland. In the interview below, Omar discusses his work in the horticulture industry as a Project Manager, touching on the state of the industry, technological trends, as well as discussing the types of projects that are interesting for him.
What is the importance of the research side of industry, how does it enhance the commercial/industrial sectors?
Optimally, research and innovation efforts should be translated into meaningful commercialized products or technologies.
Having the correct mix between an industrial engineering experience and university research experience, allows me to be perfectly aligned with Vineland’s vision to create impact for the Canadian horticulture sector.
As an independent research organization, Vineland understands the importance of business planning and commercialization for its stakeholders.
What is your process like with Vineland, what is a typical project like for you?
In general, Vineland’s research strategy incorporates four core processes: stakeholder engagement, research priorities, opportunity analysis and project management.
A typical project as part of Vineland’s Systems Integration program would entail mainly the opportunity analysis and project management processes, to ensure that all projects offer the greatest impact for the Canadian horticulture sector while remaining accountable and meeting deadlines.
What are some of the challenges you face in your role as Project Manager System Integration Robotics and Automation? How do you address them?
Technology is fast moving especially when it comes to robotics and automation. What’s important is to be constantly aware of emerging technologies and industry trends in different sectors, understand the competition and explore which technologies can be adopted by the horticulture sector and which ones are still too immature to yet be utilized.
Having the opportunity to attend a few big technology conferences each year, usually does the job in letting me know what’s going around.
Another challenge is helping producers finding customized efficient solutions from local suppliers while providing good payback and meeting customers’ needs, rather than buying “trusted brands” machines from overseas, paying extra for shipping and customs with the associated high risks of delayed technical support and sometimes incompatibility with existing systems.
What is an ideal project for you, or what types of projects do you find most interesting?
Generally, I find projects involving high-speed precision robotics for pick and place applications to be very interesting. It is amazing to imagine how much one robot with a 150 pick/minute rate can save labour and production costs in processes, such as sorting and packing fresh produce into trays.
Another type of consultation projects we provide, which is very uncommon in this industry, is the implementation of simple LEAN and waste reduction methodologies to optimize production operations, often used in the manufacturing sector, to help producers and facility owners convert their low-profit business into a high-profit efficient organization. With small tweaks in operations and sometimes by rearranging the facility layout to ensure an optimal product flow, minimal waste, and eliminate non-value-added activities, could all contribute to huge savings.
What does robotics and automation look like in the agriculture/horticulture industry, does it differ at all in how it is utilized in industrial/manufacturing settings?
There are some clear differences between robotics and automation in the horticulture and agriculture industry and how it is utilized in industrial and manufacturing settings. In horticulture almost everything is variable, either within the environment or the crop itself.
Unlike robotics and automation within factories, which deal with defined objects or manufactured components in a controlled environment, in horticulture everything from lighting, temperature, shape, size and orientation of the product is variable. For example, the integrated vision systems in most grading and sorting automated applications in horticulture are more complex in order to capture the size, colour, curvature, density, stem orientation, water content, external and internal quality within the same crop product such as apples or peaches. Also, robots used to pick and place fresh produce need to be clean, designed for a humid environment and have soft/self-morphing grippers to properly handle the products.
There is definitely a bigger challenge for horticulture and agriculture applications in making the systems reliable and smart in order to automatically deal with the vast amount of variability and uncertainty within both the crops and environment and with minimal human interference.
Could you perhaps comment on the state of automation and robotics in agriculture/horticulture; is it prominently used, are there any sticking points or barriers/what are the keys to it becoming more prominent, do the technologies need to progress to improve ROI, etc.?
Nowadays, with Canada’s high labour costs, robotics and automation are not considered “a nice to have” in our industry any longer. Robotics and precise agriculture have been gaining much attention in recent years as Canadian growers start exploring opportunities for more efficient tools and processes to reduce production costs and help overcome labour challenges.
We still can’t say that automation and related technologies are 100 per cent mature and prominently used in the horticulture industry, as can be seen for the automotive and manufacturing sectors but there is an increasing demand for integrated automation solutions as a way to leverage profits and improve competitiveness.
In horticulture, operations like sorting, grading, pot filling, labelling, box making, climate control, potting and labour management are now fully automated and widely used. However, there are many other operations that are still challenging to fully automate such as planting, harvesting, pruning and disease detection.
The main barriers for transferring or developing technologies from different industries are the growing environment, the product variability and the high uncertainty. Also, it’s important to design cost-effective automation solutions that will operate as well or better than humans.
Although robotic and sensor technologies have become more affordable, many technologies related to vision systems, grippers, precision and data analysis still need improvement and customization to help increase the ROI of the adopted solutions.
What is next for your industry? Are there any emerging technologies or trends that you see as becoming more prominent in 5-10 years or so?
Technologies for horticulture have significantly evolved in the past 10 years. Trends that have become commercially available in recent years include: smart irrigation, high-speed robotic packing and packaging, robotic transplanting and smart supplemental lighting systems. And this is thanks to huge advances in camera and vision systems, delta robots, LED technologies and internet of things (IoT)/data analysis.
The next five to 10 years will see a convergence towards smart farming and digital/precise growing where farmers will gain the ability to digitize their entire plant growth cycle indoor and have complete control over their operation.
Smart farming is a precision farming management system where technologies like sensors, automatic control systems, IoT, vision systems, artificial intelligence and machine learning are integrated together in one system to provide growers with added value in the form of accurate harvest forecast and better decision-making over production operations e.g. irrigation, climate control, lighting spectrum and intensity control, disease detection, as well as decision-making for harvesting.
What is the right question when it comes to robotics and automation in agriculture/horticulture? Is there anything I didn’t ask about that is pertinent to the industry?
I would like to point out that the agriculture and horticulture sectors in Canada are considered to be green fields when it comes to automation and robotics by local manufacturers and engineering service providers. You can definitely see a shift happening, especially from the saturated automotive industry, but there is still a need for more collaborations and investments to accelerate the pace of advancement of products and solutions made by the local agriculture industry.
Go HERE for more information on Vineland
Blake Marchand is Assistant Editor, Kerrwil Electrical Group