Navigating the Robotic Revolution – Addressing Labor Shortages with FANUC Automation Skills
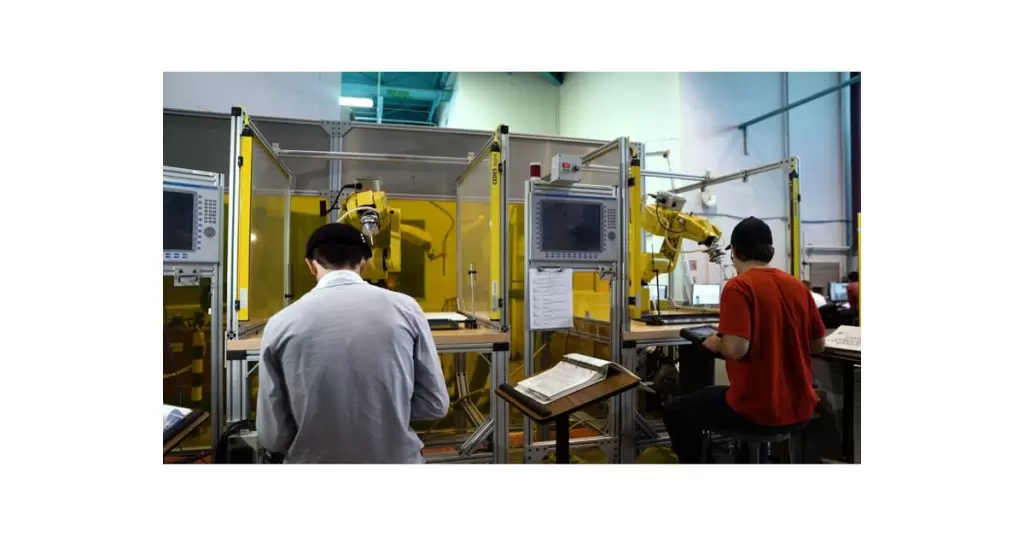
April 17, 2024
As businesses all over the world face an ever-increasing labor shortage, robotics and automation have become a popular solution. And out of the four million robots installed globally, over a quarter of them are FANUC. The ongoing challenge for most companies is finding operators who have the skills to work with robotics and automation.
For over a decade, FANUC’s education philosophy has centered on empowering the workforce to reach their goals by earning industry-recognized certifications as well as two and four-year degrees in robotics and automation.
What that means for today’s businesses is having access to a pipeline of highly skilled automation workers ready to help them achieve their goals and overcome the labor shortage.
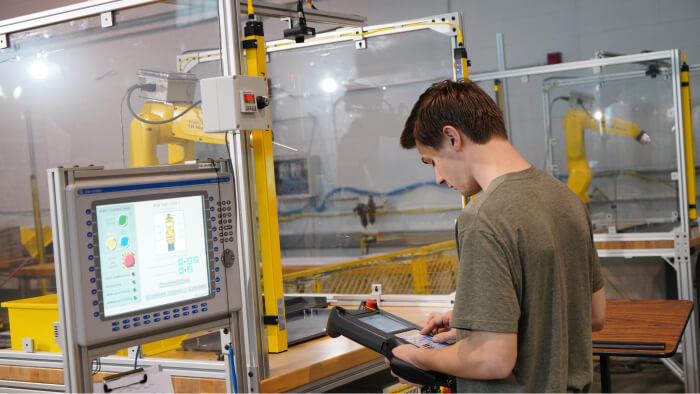
The State of Automation Training: Robot Operation to System Integration
FANUC’s early education programs focused on teaching basic robot or CNC operation. However, automation is quickly evolving because today’s robotic production cells include vision systems, sensors, AI, HMIs, and a wide range of interconnected devices. Because of this, operators need a broader skill set beyond simply knowing how to operate a robot – they need to understand the entire automation system.
In addition to robot programming, students who learn to integrate sensors, and optimize production lines are going to thrive in dynamic production environments. Their ability to handle complex systems, troubleshoot issues, and ensure seamless operations contributes significantly to effective manufacturing processes.
FANUC America offers comprehensive training programs for all aspects of automation. Whether you’re a student, operator, programmer, maintenance specialist, or designer, FANUC’s tailored courses are designed to maximize your robotics and CNC skill set.
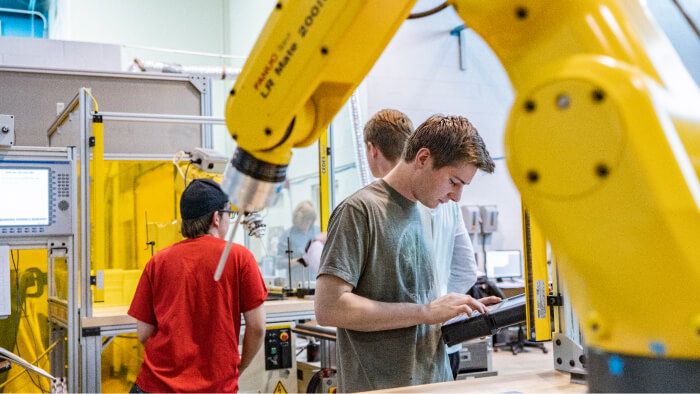
A Collaborative Approach
FANUC America collaborates with educational institutions and businesses with a dual purpose: to equip students with the skills needed to obtain stable, well-paying automation careers, and provide companies a talent pool consisting of graduates who are experts in advanced robotics and automation. To date, FANUC has collaborated with over 1,500 high schools, tech training centers, community colleges and universities to offer hands-on training for FANUC automation products. Given that FANUC is the most commonly used brand of robots and automation, the training programs fully support industry needs.
This tight collaboration between FANUC, education and industry ensures that the next generation of automation professionals will thrive and grow in a rapidly changing industry. Companies that hire employees with robotic and automation skills will achieve higher levels of operational efficiency and improve their outlook for long-term success in a technology-driven world. Here’s just some of the advantages that companies can achieve with an automation-savvy workforce:
Increased Productivity and Efficiency:
- Skilled employees can design, program, and maintain automated systems, leading to streamlined processes and higher productivity.
- Automation allows skilled workers to focus on more strategic tasks versus performing the dull, dirty, and dangerous tasks formerly associated with manufacturing.
Cost Savings:
- Efficient automation reduces operational costs by minimizing errors, waste, and downtime.
- Better resource utilization.
Improved Quality and Consistency:
- Skilled workers ensure that automated systems operate consistently.
- Quality control becomes more precise, leading to better products and services.
Safety Enhancement:
- Automation reduces the need for people to perform potentially hazardous tasks.
- Employees with automation skills contribute to safer work environments.
Innovation and Adaptability:
- Skilled workers drive innovation by integrating new technologies and optimizing existing systems.
- Employees can adapt swiftly to changing market demands.
Competitive Advantage:
- Companies that invest in automation skills training for their employees have a competitive edge.
- Having skilled employees allows you to deliver products faster, stay ahead of industry trends, and increase your ability to scale according to market demands.
Job Creation and Upskilling:
- Automation creates new roles – contrary to the false belief that robots eliminate jobs.
- Companies benefit from a workforce capable of handling advanced technologies.
Optimizing Existing Systems:
- Skilled workers understand the intricacies of existing systems, and can identify inefficiencies, bottlenecks, and areas for improvement.
Problem Solving and Innovation:
- When faced with challenges, skilled workers think creatively – they propose innovative solutions, whether it’s automating repetitive tasks or enhancing data analytics.
Enhancing Collaboration and Communication:
- Skilled workers bridge gaps between departments, ensuring smooth communication and alignment.
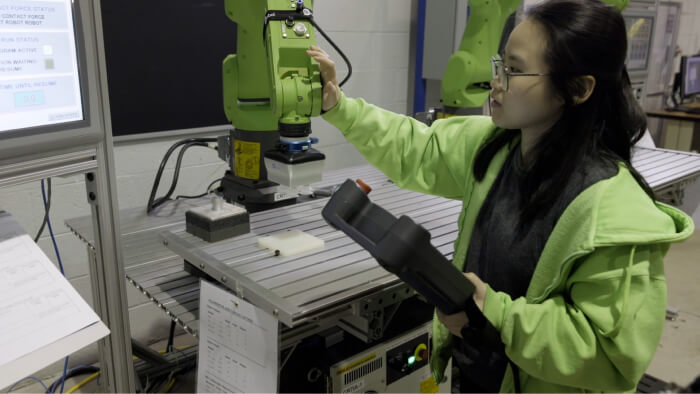
Join the Automation Generation
Skilled workers play a crucial role in driving innovation through technology integration. FANUC America’s commitment to workforce development transcends traditional training. It’s about nurturing minds, fostering innovation, and driving the future of manufacturing.
Whether you’re a manager searching for employees with advanced automation skills, a student considering your future, or you’re employed but looking for a different pathway – now is the time to join the automation generation.